Budowa maszyn CNC na zamówienie przynosi wiele korzyści, które mogą znacząco wpłynąć na efektywność produkcji w różnych branżach. Przede wszystkim, maszyny te są projektowane z myślą o specyficznych potrzebach klienta, co pozwala na optymalizację procesów produkcyjnych. Dzięki temu można osiągnąć wyższą precyzję i jakość wykonania, co jest kluczowe w branżach takich jak przemysł lotniczy, motoryzacyjny czy medyczny. Kolejną zaletą jest możliwość dostosowania maszyny do istniejących linii produkcyjnych, co minimalizuje czas przestoju i koszty związane z adaptacją. Co więcej, maszyny CNC na zamówienie często charakteryzują się nowoczesnymi rozwiązaniami technologicznymi, co przekłada się na większą wydajność i oszczędność energii. Klienci mogą także liczyć na wsparcie techniczne oraz serwis posprzedażowy, co zwiększa komfort użytkowania.
Jakie technologie są wykorzystywane w budowie maszyn CNC
W budowie maszyn CNC na zamówienie wykorzystuje się różnorodne technologie, które mają kluczowe znaczenie dla ich funkcjonalności i wydajności. Jedną z najpopularniejszych technologii jest frezowanie CNC, które pozwala na precyzyjne formowanie materiałów poprzez usuwanie nadmiaru materiału za pomocą narzędzi skrawających. Inną istotną metodą jest toczenie CNC, które umożliwia obróbkę cylindrycznych elementów z dużą dokładnością. W ostatnich latach coraz większą popularność zdobywa także technologia druku 3D, która pozwala na szybkie prototypowanie oraz produkcję skomplikowanych kształtów bez konieczności stosowania tradycyjnych narzędzi skrawających. Dodatkowo, w nowoczesnych maszynach CNC często stosuje się systemy automatycznego pomiaru i kontroli jakości, co zwiększa precyzję obróbki i minimalizuje ryzyko błędów. Warto również wspomnieć o zastosowaniu sztucznej inteligencji oraz algorytmów uczenia maszynowego, które mogą optymalizować procesy produkcyjne oraz przewidywać awarie sprzętu.
Jakie materiały można obrabiać przy użyciu maszyn CNC
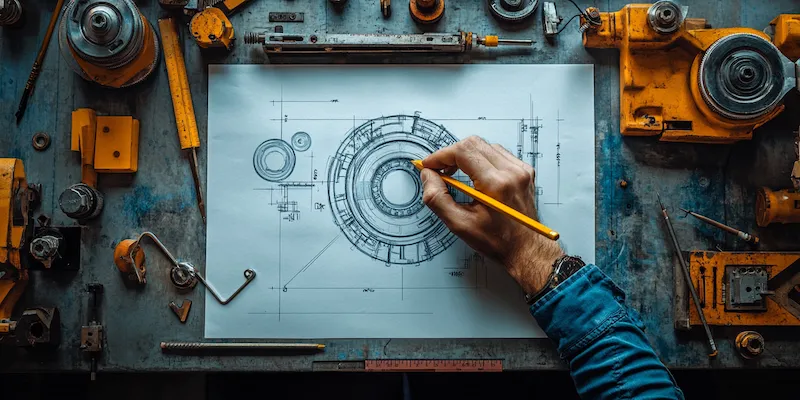
Maszyny CNC na zamówienie są niezwykle wszechstronne i mogą obrabiać różnorodne materiały, co czyni je idealnym rozwiązaniem dla wielu branż przemysłowych. Do najczęściej obrabianych materiałów należą metale takie jak stal nierdzewna, aluminium czy miedź. Te materiały są powszechnie wykorzystywane w budowie komponentów mechanicznych oraz konstrukcji maszyn. Oprócz metali, maszyny CNC doskonale radzą sobie z obróbką tworzyw sztucznych, takich jak nylon czy poliwęglan, które znajdują zastosowanie w produkcji elementów elektronicznych oraz części samochodowych. Drewno to kolejny materiał, który można obrabiać przy użyciu technologii CNC; maszyny te umożliwiają precyzyjne cięcie i frezowanie drewna, co jest istotne w meblarstwie oraz budownictwie. Coraz częściej spotyka się także obróbkę kompozytów oraz materiałów ceramicznych, które wymagają specjalistycznych narzędzi i technologii ze względu na swoją twardość i kruchość.
Jakie są koszty budowy maszyn CNC na zamówienie
Koszty budowy maszyn CNC na zamówienie mogą być bardzo zróżnicowane w zależności od wielu czynników, takich jak rodzaj maszyny, jej specyfikacja techniczna oraz zastosowane technologie. Na początku warto zwrócić uwagę na koszty projektowania i inżynieryjnego przygotowania maszyny. To etap kluczowy dla zapewnienia odpowiedniej funkcjonalności oraz wydajności urządzenia. Następnie należy uwzględnić koszty materiałów potrzebnych do produkcji maszyny; im bardziej zaawansowane technologie i materiały zostaną zastosowane, tym wyższe będą koszty. Kolejnym istotnym elementem są koszty robocizny związane z montażem i uruchomieniem maszyny; zatrudnienie wykwalifikowanych specjalistów może znacząco wpłynąć na całkowity koszt inwestycji. Nie można zapominać o kosztach związanych z serwisem posprzedażowym oraz ewentualnymi naprawami w przyszłości; dobrze jest wybierać dostawców oferujących kompleksową obsługę klienta.
Jakie są najważniejsze etapy budowy maszyn CNC na zamówienie
Budowa maszyn CNC na zamówienie to proces składający się z kilku kluczowych etapów, które mają na celu zapewnienie, że finalny produkt spełni wszystkie wymagania klienta. Pierwszym krokiem jest analiza potrzeb klienta oraz specyfikacji projektu. W tym etapie inżynierowie i projektanci współpracują z klientem, aby dokładnie zrozumieć jego oczekiwania oraz wymagania dotyczące wydajności, precyzji i funkcjonalności maszyny. Następnie przechodzi się do fazy projektowania, gdzie tworzone są szczegółowe plany techniczne oraz modele 3D maszyny. To ważny moment, ponieważ wszelkie błędy na tym etapie mogą prowadzić do problemów w późniejszych fazach produkcji. Po zatwierdzeniu projektu następuje etap produkcji, który obejmuje zarówno obróbkę materiałów, jak i montaż poszczególnych komponentów maszyny. W trakcie tego procesu kluczowe jest zachowanie wysokich standardów jakości oraz precyzji. Po zakończeniu montażu maszyna przechodzi szereg testów, które mają na celu sprawdzenie jej funkcjonalności oraz wydajności.
Jakie są najczęstsze problemy przy budowie maszyn CNC
Podczas budowy maszyn CNC na zamówienie mogą wystąpić różne problemy, które mogą wpłynąć na czas realizacji projektu oraz jakość finalnego produktu. Jednym z najczęstszych wyzwań jest niedostateczna komunikacja między zespołem projektowym a klientem. Często zdarza się, że oczekiwania klienta nie są w pełni zrozumiane lub przekazane w sposób jasny, co prowadzi do nieporozumień i konieczności wprowadzania poprawek w późniejszym etapie. Innym problemem mogą być opóźnienia w dostawie materiałów lub komponentów niezbędnych do budowy maszyny. Tego rodzaju sytuacje mogą znacząco wydłużyć czas realizacji projektu i zwiększyć koszty. Dodatkowo, trudności techniczne związane z projektowaniem lub montażem maszyny mogą prowadzić do błędów konstrukcyjnych, które będą wymagały dodatkowego czasu i zasobów na naprawę. Warto również zwrócić uwagę na kwestie związane z zapewnieniem odpowiednich norm jakościowych; brak odpowiednich certyfikatów czy spełnienia standardów może skutkować odrzuceniem maszyny przez klienta lub koniecznością przeprowadzenia dodatkowych testów.
Jakie są różnice między maszynami CNC a tradycyjnymi metodami obróbczy
Maszyny CNC różnią się od tradycyjnych metod obróbczych pod wieloma względami, co czyni je bardziej efektywnym rozwiązaniem dla wielu zastosowań przemysłowych. Przede wszystkim, maszyny CNC oferują znacznie wyższą precyzję obróbki; dzięki zastosowaniu komputerowego sterowania możliwe jest osiągnięcie tolerancji rzędu mikrometrów, co jest trudne do osiągnięcia przy użyciu tradycyjnych narzędzi ręcznych. Kolejną istotną różnicą jest automatyzacja procesu; maszyny CNC mogą pracować bez przerwy przez długi czas bez potrzeby interwencji operatora, co zwiększa wydajność produkcji i redukuje koszty pracy. Tradycyjne metody obróbcze często wymagają większej liczby pracowników oraz dłuższego czasu realizacji zamówienia. Dodatkowo, maszyny CNC umożliwiają łatwe wprowadzanie zmian w programie obróbczy, co pozwala na szybką adaptację do zmieniających się potrzeb rynku i klientów. Warto również zauważyć, że w przypadku maszyn CNC możliwe jest obrabianie skomplikowanych kształtów i detali, które byłyby trudne lub wręcz niemożliwe do wykonania za pomocą tradycyjnych metod.
Jakie są przyszłe trendy w budowie maszyn CNC na zamówienie
Przemysł maszynowy nieustannie ewoluuje i w budowie maszyn CNC na zamówienie można zaobserwować kilka istotnych trendów, które będą miały wpływ na przyszłość tej technologii. Jednym z nich jest rosnąca automatyzacja procesów produkcyjnych; coraz więcej firm inwestuje w robotyzację linii produkcyjnych oraz integrację systemów zarządzania produkcją z maszynami CNC. Dzięki temu możliwe jest osiągnięcie jeszcze wyższej wydajności oraz redukcja błędów ludzkich. Kolejnym trendem jest rozwój technologii druku 3D; wiele firm zaczyna łączyć tradycyjne metody obróbczy z drukiem addytywnym, co pozwala na tworzenie bardziej skomplikowanych struktur oraz prototypowanie nowych produktów w krótszym czasie. Warto także zwrócić uwagę na rosnącą rolę sztucznej inteligencji i analizy danych; dzięki zastosowaniu algorytmów uczenia maszynowego możliwe będzie optymalizowanie procesów produkcyjnych oraz przewidywanie awarii sprzętu przed ich wystąpieniem. Zmiany te są wynikiem rosnącej konkurencji na rynku oraz potrzeby dostosowania się do dynamicznie zmieniających się potrzeb klientów.
Jakie są przykłady zastosowania maszyn CNC w różnych branżach
Maszyny CNC znajdują szerokie zastosowanie w różnych branżach przemysłowych dzięki swojej wszechstronności i precyzji obróbczy. W przemyśle motoryzacyjnym wykorzystuje się je do produkcji komponentów silników, karoserii czy elementów zawieszenia; dzięki technologii CNC możliwe jest osiągnięcie wysokiej jakości wykonania oraz powtarzalności procesów produkcyjnych. W branży lotniczej maszyny te są wykorzystywane do obróbki skomplikowanych części samolotowych, takich jak elementy skrzydeł czy silników odrzutowych; precyzyjne wykonanie tych komponentów ma kluczowe znaczenie dla bezpieczeństwa lotu. W przemyśle medycznym maszyny CNC służą do produkcji implantów oraz narzędzi chirurgicznych; ich wysoka dokładność pozwala na tworzenie elementów o skomplikowanej geometrii dostosowanej do indywidualnych potrzeb pacjentów. Ponadto, w meblarstwie wykorzystuje się maszyny CNC do cięcia i frezowania drewna oraz materiałów kompozytowych; umożliwia to szybkie tworzenie unikalnych projektów mebli o wysokiej estetyce wykonania.
Jakie umiejętności są potrzebne do pracy z maszynami CNC
Aby skutecznie pracować z maszynami CNC na zamówienie, niezbędne są różnorodne umiejętności techniczne oraz wiedza specjalistyczna. Kluczową kompetencją jest znajomość programowania maszyn CNC; operatorzy muszą umieć pisać i edytować programy sterujące urządzeniami, co wymaga dobrej znajomości języków programowania takich jak G-code czy M-code. Ponadto istotna jest umiejętność czytania rysunków technicznych oraz schematów CAD; operatorzy muszą być w stanie interpretować dokumentację projektową i przekształcać ją w konkretne działania obróbcze. Wiedza z zakresu technologii materiałowej również odgrywa ważną rolę; operatorzy powinni znać właściwości różnych materiałów oraz techniki ich obróbki, aby móc dostosować parametry pracy maszyny do specyfiki danego materiału. Dodatkowo umiejętności analityczne są niezbędne do rozwiązywania problemów technicznych oraz optymalizacji procesów produkcyjnych; operatorzy muszą być gotowi do szybkiego reagowania na ewentualne awarie czy błędy podczas pracy maszyny.