Destylacja rozpuszczalników jest procesem, który polega na oddzieleniu składników mieszaniny na podstawie różnicy ich temperatur wrzenia. W tym procesie wykorzystuje się zjawisko parowania i skraplania, co pozwala na uzyskanie czystych substancji chemicznych. Kluczowym elementem destylacji jest kolumna destylacyjna, która umożliwia wielokrotne parowanie i skraplanie, co zwiększa efektywność separacji. W praktyce najpierw podgrzewa się mieszaninę, a składniki o niższej temperaturze wrzenia przechodzą w stan gazowy. Następnie para jest kierowana do chłodnicy, gdzie skrapla się z powrotem w ciecz. Ważnym aspektem jest również dobór odpowiednich warunków procesu, takich jak ciśnienie atmosferyczne, które wpływa na temperatury wrzenia poszczególnych składników. W przypadku rozpuszczalników organicznych często stosuje się destylację prostą lub frakcyjną, w zależności od ich właściwości fizykochemicznych.
Jakie są różnice między destylacją prostą a frakcyjną
Destylacja prosta i frakcyjna to dwa podstawowe rodzaje procesów destylacyjnych, które różnią się zarówno w metodzie wykonania, jak i zastosowaniem. Destylacja prosta jest najczęściej stosowana do separacji substancji o znacznie różniących się temperaturach wrzenia. Proces ten polega na jednorazowym podgrzewaniu mieszaniny i zbieraniu pary, która skrapla się w chłodnicy. Jest to metoda stosunkowo szybka i łatwa do przeprowadzenia, jednak jej efektywność maleje przy niewielkich różnicach temperatur wrzenia składników. Z kolei destylacja frakcyjna jest bardziej skomplikowanym procesem, który wykorzystuje kolumnę frakcyjną do wielokrotnego parowania i skraplania. Dzięki temu możliwe jest uzyskanie wyższej czystości produktów oraz skuteczniejsze oddzielanie składników o zbliżonych temperaturach wrzenia. W praktyce destylacja frakcyjna jest często wykorzystywana w przemyśle petrochemicznym oraz przy produkcji alkoholu wysokoprocentowego.
Jakie są zastosowania destylacji rozpuszczalników w przemyśle
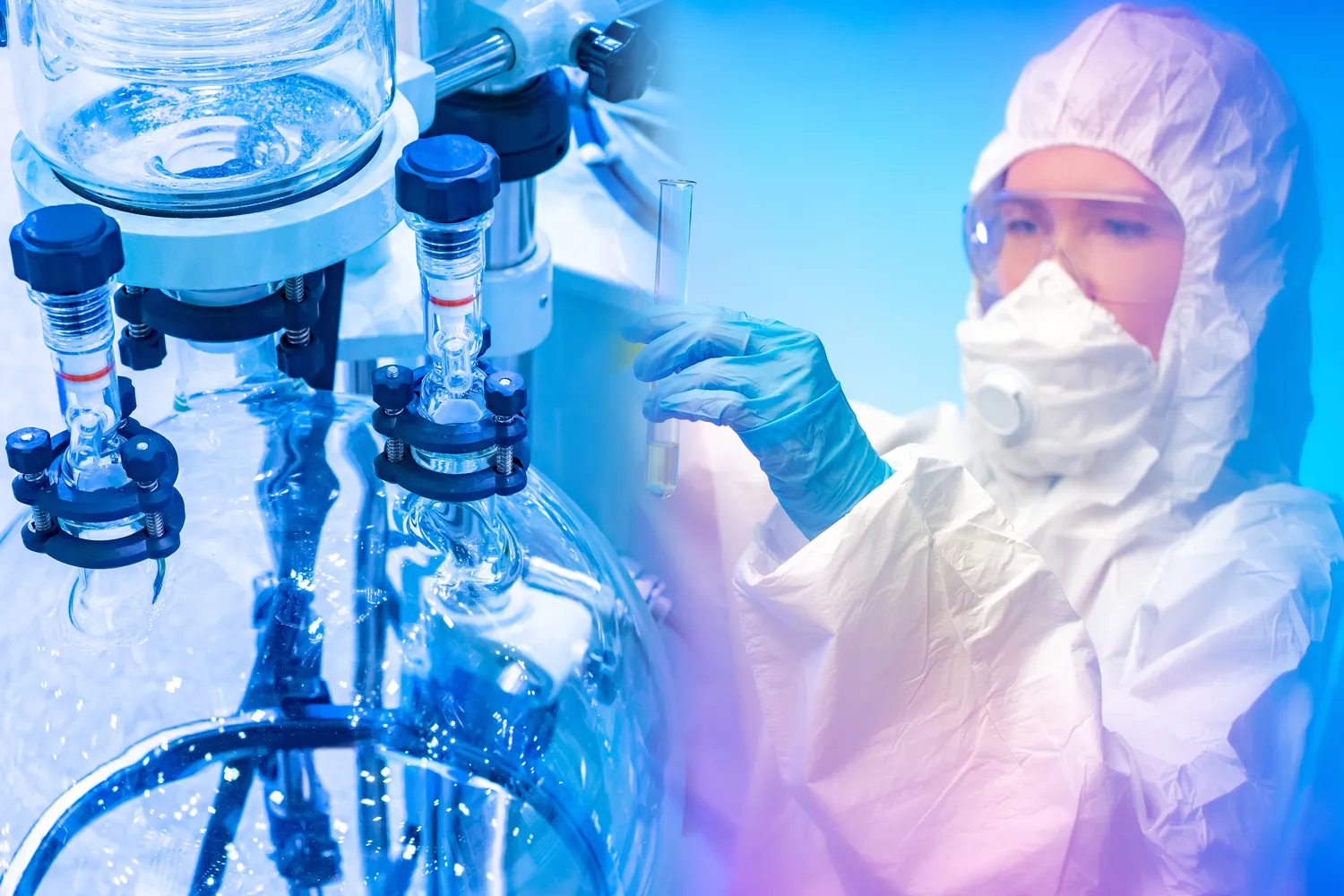
Destylacja rozpuszczalników ma szerokie zastosowanie w różnych gałęziach przemysłu, co czyni ją kluczowym procesem technologicznym. W przemyśle chemicznym destylacja służy do oczyszczania surowców oraz produktów końcowych z niepożądanych zanieczyszczeń. Na przykład w produkcji farb i lakierów wykorzystuje się destylację do usuwania rozpuszczalników organicznych, co pozwala na uzyskanie wysokiej jakości produktów gotowych. W branży farmaceutycznej proces ten jest niezbędny do izolacji aktywnych substancji czynnych z surowców naturalnych lub syntetycznych. Dzięki destylacji można również uzyskać czyste rozpuszczalniki do dalszych reakcji chemicznych lub analiz laboratoryjnych. Ponadto w przemyśle spożywczym destylacja znajduje zastosowanie przy produkcji alkoholi oraz ekstraktów roślinnych, gdzie kluczowe jest zachowanie aromatów i smaków.
Jakie są najważniejsze czynniki wpływające na efektywność destylacji
Efektywność procesu destylacji rozpuszczalników zależy od wielu czynników, które mogą znacząco wpłynąć na jakość uzyskiwanych produktów oraz wydajność całego procesu. Pierwszym z nich jest temperatura podgrzewania mieszaniny; zbyt niska temperatura może prowadzić do niepełnej separacji składników, natomiast zbyt wysoka może powodować degradację termiczną substancji. Kolejnym istotnym elementem jest ciśnienie atmosferyczne; obniżenie ciśnienia pozwala na obniżenie temperatury wrzenia substancji, co może być korzystne dla materiałów wrażliwych na wysoką temperaturę. Ważną rolę odgrywa także konstrukcja kolumny destylacyjnej; jej długość oraz liczba teoretycznych półek wpływają na liczbę cykli parowania i skraplania, co przekłada się na czystość końcowego produktu. Dodatkowo właściwości fizykochemiczne składników mieszaniny, takie jak ich polarność czy lepkość, mogą wpływać na przebieg procesu i jego efektywność.
Jakie są najczęstsze problemy podczas destylacji rozpuszczalników
Podczas destylacji rozpuszczalników mogą wystąpić różne problemy, które mogą wpłynąć na jakość i wydajność procesu. Jednym z najczęstszych problemów jest tworzenie się piany w kolumnie destylacyjnej, co może prowadzić do zatykania rur oraz obniżenia efektywności separacji. Piana powstaje zazwyczaj w wyniku reakcji chemicznych lub obecności substancji powierzchniowo czynnych w mieszaninie. Aby temu zapobiec, można zastosować odpowiednie środki antypieniące lub dostosować warunki operacyjne, takie jak temperatura i ciśnienie. Innym problemem jest niepełna separacja składników, co może być spowodowane niewłaściwym doborem kolumny destylacyjnej lub zbyt małą różnicą temperatur wrzenia między składnikami. W takich przypadkach konieczne może być zwiększenie długości kolumny lub zastosowanie destylacji frakcyjnej. Dodatkowo, zanieczyszczenia w surowcach mogą prowadzić do niepożądanych reakcji chemicznych, które wpływają na jakość końcowego produktu.
Jakie są nowoczesne technologie stosowane w destylacji rozpuszczalników
W ostatnich latach rozwój technologii destylacyjnych znacząco wpłynął na efektywność procesów związanych z destylacją rozpuszczalników. Nowoczesne systemy wykorzystują zaawansowane metody, takie jak destylacja membranowa czy destylacja z wykorzystaniem ultradźwięków, które oferują wyższą wydajność oraz mniejsze zużycie energii. Destylacja membranowa polega na wykorzystaniu selektywnych membran do separacji składników mieszaniny, co pozwala na uzyskanie wysokiej czystości produktów bez potrzeby stosowania wysokich temperatur. Z kolei destylacja ultradźwiękowa wykorzystuje fale dźwiękowe do wzmacniania procesu parowania, co przyspiesza separację składników i zmniejsza czas trwania całego procesu. Inną innowacyjną metodą jest destylacja azeotropowa, która pozwala na skuteczne oddzielanie składników w przypadku mieszanin azeotropowych, gdzie tradycyjne metody mogą być nieskuteczne.
Jakie są kluczowe aspekty bezpieczeństwa podczas destylacji rozpuszczalników
Bezpieczeństwo podczas destylacji rozpuszczalników jest niezwykle istotnym zagadnieniem, które należy uwzględnić na każdym etapie procesu. Przede wszystkim ważne jest zapewnienie odpowiedniej wentylacji w pomieszczeniu, w którym odbywa się destylacja, aby uniknąć gromadzenia się szkodliwych oparów chemicznych. Używanie odpowiednich środków ochrony osobistej, takich jak rękawice, okulary ochronne oraz odzież robocza, jest niezbędne dla ochrony pracowników przed potencjalnymi zagrożeniami. Kolejnym kluczowym aspektem jest monitorowanie temperatury i ciśnienia w systemie; nagłe zmiany tych parametrów mogą prowadzić do niebezpiecznych sytuacji, takich jak eksplozje czy pożary. Dlatego zaleca się stosowanie urządzeń zabezpieczających oraz systemów alarmowych, które będą informować o nieprawidłowościach w czasie rzeczywistym. Ważne jest również przeprowadzanie regularnych szkoleń dla pracowników dotyczących procedur awaryjnych oraz zasad postępowania w przypadku wystąpienia incydentów związanych z bezpieczeństwem.
Jakie są ekologiczne aspekty związane z procesem destylacji
Ekologiczne aspekty związane z procesem destylacji rozpuszczalników stają się coraz bardziej istotne w kontekście rosnącej świadomości ekologicznej oraz regulacji prawnych dotyczących ochrony środowiska. Proces ten często wiąże się z dużym zużyciem energii oraz emisją szkodliwych substancji do atmosfery i wód gruntowych. Dlatego wiele firm stara się wdrażać rozwiązania mające na celu minimalizację negatywnego wpływu na środowisko. Przykładem takiego podejścia jest recykling rozpuszczalników; dzięki zastosowaniu technologii odzysku możliwe jest ponowne wykorzystanie substancji chemicznych zamiast ich utylizacji. Warto również zwrócić uwagę na rozwój bardziej ekologicznych metod separacji, takich jak wspomniana wcześniej destylacja membranowa czy inne technologie alternatywne, które generują mniejsze ilości odpadów oraz zużywają mniej energii. Ponadto wiele przedsiębiorstw inwestuje w systemy monitorowania emisji oraz zarządzania odpadami chemicznymi, co pozwala na lepsze zarządzanie procesami produkcyjnymi i ich wpływem na środowisko naturalne.
Jakie są przyszłościowe kierunki badań nad destylacją rozpuszczalników
Przyszłościowe kierunki badań nad destylacją rozpuszczalników koncentrują się na poszukiwaniu bardziej efektywnych i ekologicznych metod separacji składników chemicznych. W miarę jak rośnie zapotrzebowanie na czyste substancje chemiczne oraz ograniczenie negatywnego wpływu przemysłu na środowisko, naukowcy poszukują innowacyjnych rozwiązań technologicznych. Jednym z obszarów badań jest rozwój nowych materiałów filtracyjnych i membranowych, które mogłyby zwiększyć efektywność procesów separacyjnych przy jednoczesnym zmniejszeniu zużycia energii. Również badania nad zastosowaniem nanotechnologii w procesach destylacyjnych stają się coraz bardziej popularne; nanomateriały mogą poprawić właściwości fizykochemiczne używanych substancji i zwiększyć ich wydajność separacyjną. Inny kierunek badań to integracja procesów chemicznych z technologiami odnawialnymi; wykorzystanie energii słonecznej czy geotermalnej do podgrzewania mieszanin może znacząco obniżyć koszty energetyczne i zmniejszyć emisję gazów cieplarnianych.
Jakie są kluczowe czynniki ekonomiczne w procesie destylacji
Ekonomiczne aspekty destylacji rozpuszczalników mają ogromne znaczenie dla przedsiębiorstw, które muszą balansować między kosztami produkcji a jakością końcowych produktów. Koszty energii stanowią jeden z najważniejszych czynników wpływających na rentowność procesu; dlatego wiele firm inwestuje w technologie zwiększające efektywność energetyczną, takie jak odzysk ciepła czy automatyzacja procesów. Dodatkowo, ceny surowców chemicznych mogą się znacznie różnić w zależności od rynku, co wpływa na koszty produkcji. Warto również zwrócić uwagę na regulacje prawne dotyczące ochrony środowiska, które mogą generować dodatkowe koszty związane z przestrzeganiem norm emisji czy zarządzaniem odpadami. Dlatego przedsiębiorstwa muszą nie tylko dążyć do optymalizacji procesów, ale także do innowacji technologicznych, które mogą obniżyć koszty operacyjne.