Destylator przemysłowy to urządzenie służące do separacji składników cieczy na podstawie różnicy w ich temperaturach wrzenia. Proces ten jest kluczowy w wielu branżach, takich jak chemiczna, petrochemiczna czy spożywcza. Destylacja polega na podgrzewaniu mieszaniny cieczy, co powoduje, że składniki o niższej temperaturze wrzenia przechodzą w stan gazowy, a następnie są skraplane i zbierane w osobnym naczyniu. W przemyśle stosuje się różne rodzaje destylatorów, w tym destylatory prostokątne, kolumnowe oraz frakcyjne. Każdy z tych typów ma swoje unikalne zastosowania i zalety. Na przykład destylatory kolumnowe są często wykorzystywane do produkcji alkoholu, ponieważ pozwalają na uzyskanie wyższej czystości produktu końcowego. W przypadku destylacji frakcyjnej możliwe jest oddzielenie wielu składników z jednego surowca, co czyni ją niezwykle efektywną w przemyśle chemicznym.
Jakie są główne zastosowania destylatorów przemysłowych
Destylatory przemysłowe mają szeroki zakres zastosowań w różnych branżach. W przemyśle chemicznym są wykorzystywane do produkcji substancji chemicznych, takich jak rozpuszczalniki czy kwasy. W branży petrochemicznej destylacja jest kluczowym procesem przy produkcji paliw, gdzie surowa ropa naftowa jest poddawana destylacji w celu uzyskania benzyny, oleju napędowego oraz innych frakcji. W przemyśle spożywczym destylatory służą do produkcji alkoholu oraz ekstraktów smakowych. Na przykład w produkcji whisky stosuje się destylację wielokrotną, aby uzyskać pożądany profil smakowy trunku. Ponadto destylatory znajdują zastosowanie w laboratoriach analitycznych do oczyszczania reagentów oraz izolacji związków chemicznych. W ostatnich latach rośnie również zainteresowanie wykorzystaniem destylacji do odzyskiwania rozpuszczalników z odpadów przemysłowych, co przyczynia się do ochrony środowiska i zrównoważonego rozwoju.
Jakie są najważniejsze rodzaje destylatorów przemysłowych
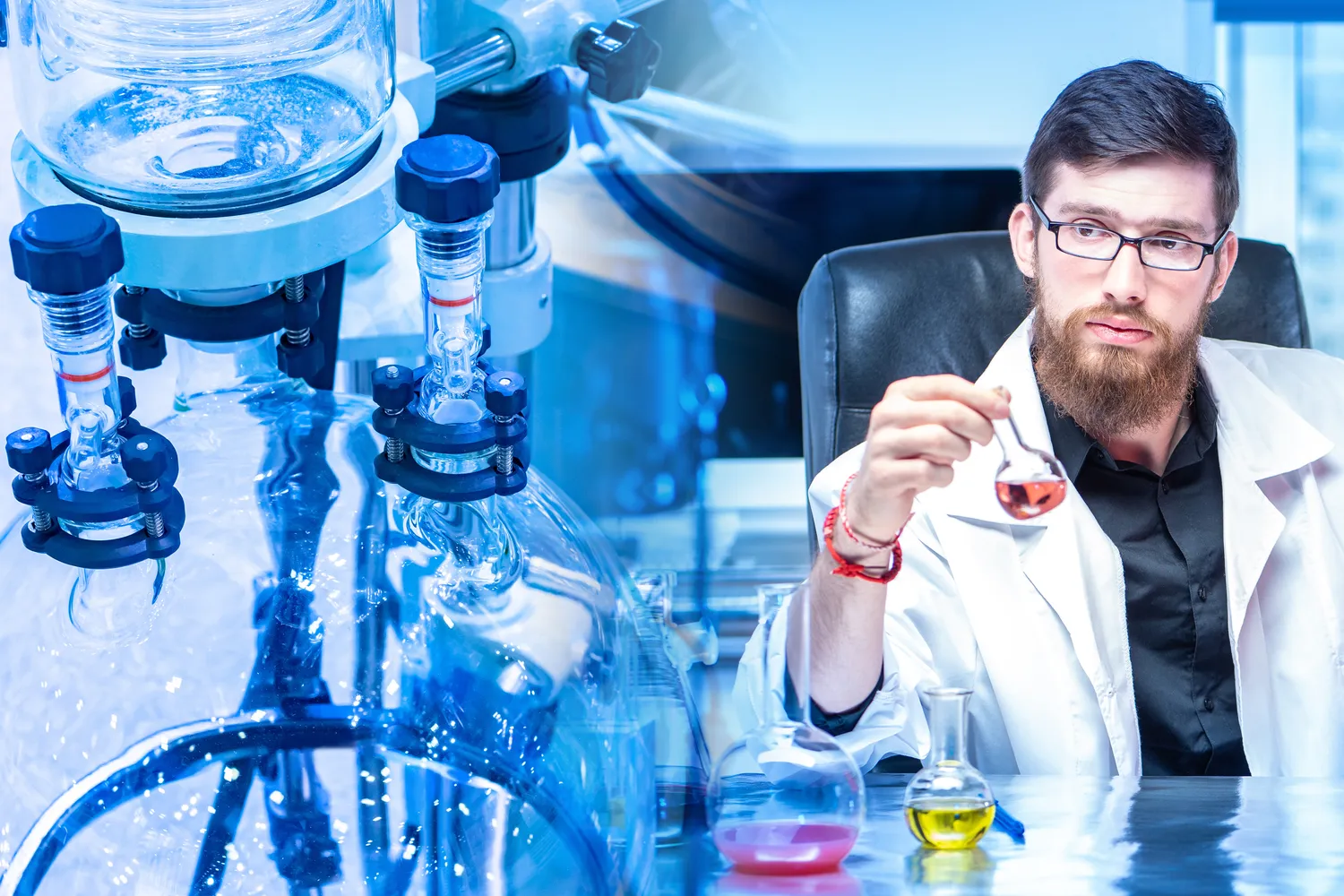
W przemyśle istnieje wiele rodzajów destylatorów, które różnią się konstrukcją oraz zasadą działania. Najpopularniejsze z nich to destylatory prostokątne, kolumnowe oraz frakcyjne. Destylatory prostokątne są najprostsze w budowie i najczęściej stosowane do małych serii produkcyjnych lub w laboratoriach. Działają na zasadzie jednofazowej destylacji i są idealne do separacji składników o znacznej różnicy temperatur wrzenia. Z kolei destylatory kolumnowe charakteryzują się bardziej skomplikowaną budową i umożliwiają wielokrotne skraplanie pary, co pozwala na uzyskanie wyższej czystości produktu końcowego. Są one powszechnie stosowane w produkcji alkoholu oraz chemikaliów. Destylatory frakcyjne natomiast pozwalają na oddzielanie wielu składników z jednej mieszaniny dzięki zastosowaniu kolumny frakcyjnej, która zwiększa efektywność procesu separacji.
Jakie są kluczowe elementy budowy destylatora przemysłowego
Budowa destylatora przemysłowego składa się z kilku kluczowych elementów, które zapewniają prawidłowe funkcjonowanie urządzenia. Podstawowym elementem jest zbiornik na ciecz, który jest podgrzewany do odpowiedniej temperatury. W przypadku destylatorów kolumnowych istotną rolę odgrywa kolumna frakcyjna, która zwiększa powierzchnię kontaktu między parą a cieczą, co pozwala na skuteczniejsze oddzielanie składników. Kolejnym ważnym elementem jest kondensator, który schładza parę i zamienia ją z powrotem w ciecz. Kondensator może mieć różne formy, ale jego zadaniem jest efektywne usuwanie ciepła z pary. Dodatkowo systemy sterowania i monitoringu są niezbędne do kontrolowania parametrów pracy destylatora, takich jak temperatura czy ciśnienie. Odpowiednia izolacja termiczna również ma znaczenie dla efektywności energetycznej urządzenia.
Jakie są nowoczesne technologie stosowane w destylacji przemysłowej
Nowoczesne technologie stosowane w procesach destylacyjnych znacząco poprawiają efektywność i jakość produktów końcowych. Jednym z najnowszych osiągnięć jest zastosowanie technologii membranowej, która pozwala na separację składników bez konieczności podgrzewania cieczy do wysokich temperatur. Ta metoda jest bardziej energooszczędna i minimalizuje ryzyko degradacji termicznej produktów. Kolejnym innowacyjnym rozwiązaniem są systemy automatyzacji procesów, które umożliwiają precyzyjne sterowanie parametrami pracy destylatora oraz monitorowanie jego wydajności w czasie rzeczywistym. Dzięki temu można szybko reagować na zmiany warunków pracy i optymalizować procesy produkcyjne. Również rozwój materiałów odpornych na korozję i wysokie temperatury przyczynia się do zwiększenia trwałości urządzeń oraz obniżenia kosztów eksploatacyjnych.
Jakie są koszty eksploatacji destylatora przemysłowego
Koszty eksploatacji destylatora przemysłowego mogą być zróżnicowane i zależą od wielu czynników, takich jak typ urządzenia, skala produkcji oraz rodzaj przetwarzanych surowców. Jednym z głównych wydatków jest energia potrzebna do podgrzewania cieczy, co może stanowić znaczną część całkowitych kosztów operacyjnych. W przypadku dużych zakładów przemysłowych, gdzie destylacja odbywa się na dużą skalę, optymalizacja zużycia energii staje się kluczowym elementem zarządzania kosztami. Warto również zwrócić uwagę na koszty związane z konserwacją i serwisowaniem urządzeń. Regularne przeglądy techniczne oraz wymiana zużytych części mogą generować dodatkowe wydatki, które należy uwzględnić w budżecie operacyjnym. Dodatkowo, w przypadku stosowania nowoczesnych technologii, takich jak automatyzacja procesów czy systemy monitoringu, mogą wystąpić koszty związane z wdrożeniem i utrzymaniem tych rozwiązań.
Jakie są najważniejsze czynniki wpływające na efektywność destylacji
Efektywność procesu destylacji jest kluczowa dla uzyskania wysokiej jakości produktów końcowych oraz minimalizacji strat surowców. Istnieje wiele czynników, które mają wpływ na tę efektywność. Przede wszystkim temperatura i ciśnienie są fundamentalnymi parametrami, które należy precyzyjnie kontrolować. Zbyt niska temperatura może prowadzić do niepełnej separacji składników, podczas gdy zbyt wysoka może powodować degradację produktów. Kolejnym istotnym czynnikiem jest czas kontaktu pary z cieczą w kolumnie frakcyjnej. Optymalizacja tego czasu pozwala na zwiększenie wydajności separacji. Również jakość używanych surowców ma znaczenie; zanieczyszczenia mogą wpłynąć na proces destylacji i obniżyć jakość finalnego produktu. Dodatkowo konstrukcja samego destylatora oraz zastosowane materiały mają wpływ na efektywność energetyczną i trwałość urządzenia.
Jakie są różnice między destylacją prostą a frakcyjną
Destylacja prosta i frakcyjna to dwa podstawowe rodzaje procesów destylacyjnych, które różnią się zarówno zasadą działania, jak i zastosowaniem. Destylacja prosta polega na jednofazowej separacji składników cieczy na podstawie różnicy temperatur wrzenia. Jest to metoda stosunkowo łatwa w realizacji i najczęściej wykorzystywana do oddzielania substancji o znacznej różnicy temperatur wrzenia. Z kolei destylacja frakcyjna jest bardziej skomplikowanym procesem, który umożliwia separację wielu składników z jednej mieszaniny dzięki zastosowaniu kolumny frakcyjnej. W tej metodzie para przechodzi przez kolumnę wielokrotnie, co pozwala na uzyskanie wyższej czystości poszczególnych frakcji. Destylacja frakcyjna jest szczególnie przydatna w przemyśle chemicznym oraz petrochemicznym, gdzie konieczne jest oddzielanie wielu składników o zbliżonych temperaturach wrzenia.
Jakie są wyzwania związane z obsługą destylatorów przemysłowych
Obsługa destylatorów przemysłowych wiąże się z wieloma wyzwaniami, które mogą wpływać na bezpieczeństwo pracy oraz jakość produktów końcowych. Jednym z głównych problemów jest kontrola parametrów pracy urządzenia, takich jak temperatura czy ciśnienie. Niewłaściwe ustawienia mogą prowadzić do nieefektywnej separacji składników lub nawet do awarii sprzętu. Ponadto operatorzy muszą być dobrze przeszkoleni w zakresie obsługi urządzeń oraz procedur bezpieczeństwa, aby minimalizować ryzyko wypadków i awarii. Inne wyzwanie to konieczność regularnego serwisowania i konserwacji sprzętu, co wiąże się z dodatkowymi kosztami oraz przestojami w produkcji. Dodatkowo zmiany w składzie surowców mogą wpłynąć na stabilność procesu destylacyjnego, co wymaga elastyczności i umiejętności dostosowywania parametrów pracy urządzenia do aktualnych warunków.
Jakie są przyszłościowe kierunki rozwoju technologii destylacyjnych
Przyszłość technologii destylacyjnych zapowiada się obiecująco dzięki dynamicznemu rozwojowi innowacyjnych rozwiązań inżynieryjnych oraz rosnącemu zainteresowaniu ekologicznymi metodami produkcji. Wśród najważniejszych kierunków rozwoju można wymienić automatyzację procesów oraz zastosowanie sztucznej inteligencji do optymalizacji pracy destylatorów. Dzięki tym technologiom możliwe będzie precyzyjne monitorowanie parametrów pracy oraz automatyczne dostosowywanie ich do aktualnych warunków operacyjnych, co zwiększy efektywność energetyczną i jakość produktów końcowych. Również rozwój materiałów odpornych na wysokie temperatury i korozję przyczyni się do zwiększenia trwałości urządzeń oraz obniżenia kosztów eksploatacyjnych. Ponadto rośnie zainteresowanie ekologicznymi metodami odzyskiwania surowców z odpadów przemysłowych poprzez zaawansowane procesy destylacyjne, co wpisuje się w globalne trendy zrównoważonego rozwoju i ochrony środowiska.